How are Diecast Cars Made? An Inside Look at the Fascinating Process
- Danny Abramovich
- Jan 2
- 3 min read
Updated: Jan 5
Diecast car models are a staple of any model vehicle collector's cabinet, cherished for their precision and the nostalgia they invoke. These miniature replicas are more than just toys; they are a result of intricate craftsmanship and industrial magic. In this article, we’ll explore the detailed process of how diecast cars are made, from conception to the final product that ends up on display shelves.
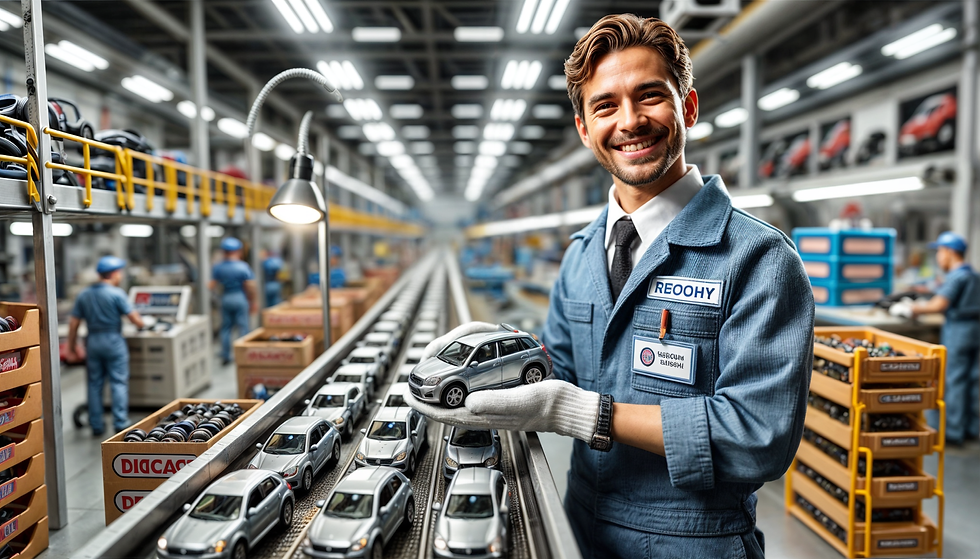
The Concept and Design Phase
The journey of a diecast car begins with the design phase. Manufacturers start by selecting a real vehicle to model. This could be a vintage classic, a modern sports car, or even a popular movie vehicle. The goal is to replicate the car in a smaller scale as accurately as possible.
To prepare for this, designers gather detailed blueprints, photographs, and actual measurements of the original car. Using sophisticated software, such as CAD (Computer-Aided Design), they create a digital model. This model is crucial as it details every aspect of the car, including the chassis, engine, interior, and even the smallest features like logos and decals.
Creating the Mold
Once the digital model is finalized, the next step is to create the molds that will shape the car's metal parts. Mold making is a precision task that requires skilled craftsmanship and technology. A CNC (Computer Numerical Control) machine carves the design into steel blocks to create these molds. The level of detail in the mold is paramount as it directly affects the quality of the final product.
The creation of molds is one of the most costly parts of the manufacturing process because of the precision and material required. For large-scale production, multiple molds are made for different parts of the car like the body, doors, and wheels.
The Diecasting Process
Diecasting is the core of the manufacturing process for these model cars. It involves casting metal under high pressure into steel molds, a method particularly suitable for zinc alloys, which are commonly used due to their strength and durability.
The diecasting machine heats the metal until it's molten. Then, it injects the molten metal into the mold at high pressures. This ensures the metal fills every part of the mold, capturing the intricacies of the design. After the metal cools and solidifies, the parts are ejected from the mold. This process is capable of producing high volumes of parts with consistency and high fidelity to the original design.
Trimming and Cleaning Up
After casting, the individual parts of the diecast cars have excess metal called flash that must be trimmed off. This is usually done using a combination of manual techniques and automated machinery. The parts are also smoothed and cleaned to prepare for assembly. It’s crucial that each part fits together perfectly to ensure the final product meets quality standards.
Assembly and Detailing
The assembly of diecast cars can be quite labor-intensive, especially for models that boast a high degree of detail. Parts like the body, interior seats, dashboard, wheels, and even tiny mirrors and lights are carefully assembled by skilled workers. Some parts are snapped together, while others require gluing.
Once assembled, the car undergoes detailing, which brings it to life. Details such as painting, decals, and chrome finishes are applied. Paint applications might involve multiple layers to achieve the right color and finish. Decals, which include tiny badges and license plates, are applied with precision. This phase of production is where the model truly starts to resemble its full-sized counterpart.
Quality Control
Quality control is integral throughout the manufacturing process but is especially rigorous before the final product is approved for sale. Each car is inspected for defects in assembly, painting, and detailing. The wheels are checked to ensure they turn freely, doors open and close smoothly, and the paint is flawless.
Packaging
The final step in the production of diecast cars is packaging. Packaging not only protects the model but also serves as a critical marketing tool. It provides information about the car model, the scale, and the brand. Often, packaging is designed to be visually appealing to attract collectors and enthusiasts.
The Role of Technology and Innovation
Over the years, the process of making diecast cars has evolved significantly. Advances in technology, such as 3D printing and automated painting, have refined the steps involved and improved the quality of the final products. Manufacturers continually innovate to create models that are more detailed and more closely mimic their real-world counterparts.
Conclusion
The creation of a diecast car is a blend of art and engineering, a process that turns simple zinc alloy into miniature masterpieces. For collectors, understanding the meticulous process behind each model can enhance the appreciation of their collections. As technology advances, so too will the precision and detail of diecast cars, making each model not just a toy but a piece of art to be treasured.
nging these small-scale marvels to life.
Comments